An EPD is a third-party verified “nutrition label” for the environmental impacts of your product, and the process for getting one is similar. You will need:
- Sustainability professional(s) to help you analyze the data and generate a report.
- A Program Operator to verify and publish your declaration.
- Data about the inputs to your product, energy consumed, and any chemical process emissions.
- A set of Product Category Rules (PCR) under which to standardize your declaration.
One difference from nutrition labels is that an EPD describes emissions that are no longer IN the product, but rather have been released to the environment. This is why transparency and verification are so important in using EPDs to make informed sustainability decisions.
Sustainability Professionals and Program Operators
EC3 maintains a list of service providers who help manufacturers through the process of creating Product EPDs or industry associations with creating Industry EPDs. (You will need to sign into EC3 to access these lists, because they are continuously updated.) Most of these service providers will be familiar with all the steps, and have contacts to help with the steps they do not cover. We advise manufacturers to work with qualified service providers who understand your specific industry well. EC3’s lists are broken out by product category, which can serve as a starting point. EC3 works with all qualified service providers without charge; a provider’s presence (or not) in this list indicates only whether EC3 has successfully digitized EPD(s) in the relevant category from that service provider. Costs and quality can vary a great deal, but EC3 does not provide information on cost or quality.
Sidebar: Product EPDs vs. Industry EPDs
Product EPDs describe the impacts of product(s) from a single manufacturer, and ideally a single facility and product. Product EPDs are the primary focus of EC3 and are further categorized for transparency and specificity.
An Industry EPD (aka sector or generic EPD) provides typical footprints for a product type across an entire industry sector. This type of EPD is typically published by a trade association based on confidential data from member manufacturers, typically weighted by market volume. Industry EPDs provide useful benchmarks of where the industry is as a whole and can be used to set realistic targets for manufacturers interested in reducing their products’ environmental footprint. It is not unusual for specific products to vary 40% or more from the most relevant industry average, so EC3 treats each industry EPD as representing the center of a range. When a supplier lacks a product EPD, EC3 assigns that product a conservative estimate of impact, a value on the high side of the industry. This process is called 'placing the burden of doubt on the declarer' and is why a most manufacturers will benefit from a product-specific EPD.

Performing Life Cycle Assessment (LCA)
What is Life Cycle Assessment?
LCA is the study of environmental impacts of products & processes based on resource consumption, emissions, and wastes throughout their life cycle. This includes all life cycle stages from production, construction, use, and to end-of-life and beyond. Some EPDs only cover the product stage while others include construction, use, and end-of-life stages as well; the scope is defined in a Product Category Rule.
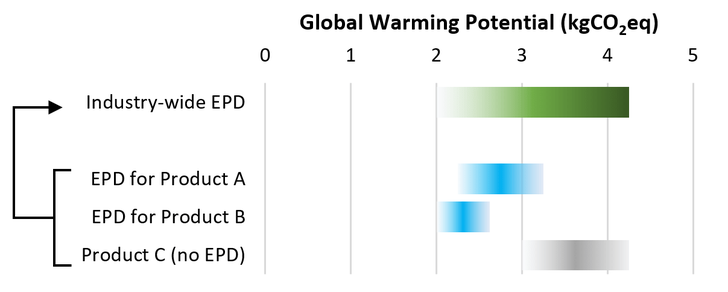
Product Category Rules (PCRs)
A Product Category Rule (PCR) defines sector-specific rules meant to ensure reasonably accurate data and fair comparisons. PCRs in turn must comply with general LCA standards. Comparing results generated under different PCRs (or extremely generic ones) can be misleading, and should be done with caution.
If a PCR does not yet exist for your product category, you may reach out to an industry association, other manufacturers, LCA service providers, or Program Operators to initiate the development of one. You can also reach out to our team, and we can help get these conversations started.
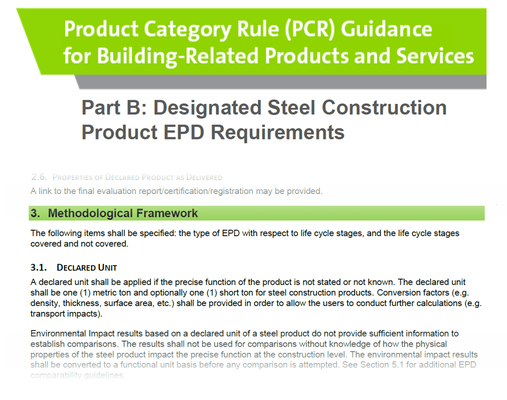
Collecting Information
The data points required for an EPD (material inputs, energy inputs, and process outputs), as defined in the PCR, are typically already tracked by manufacturers for cost, QA, and regulatory purposes, so the additional effort need not be large. The data can be collected by in-house staff or outsourced to an LCA service provider, but must be verifiable by a third party.
For facilities that produce many versions of a similar product (e.g. concrete mixes), it is often worth creating and verifying a reusable LCA model, from which product EPDs can be automatically generated.
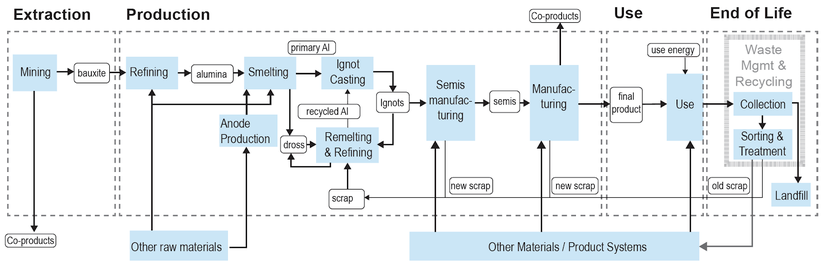
Commercial Confidentiality
Generating the Life Cycle Assessment report required to create an EPD often requires access to proprietary information, such as product formulations, supplier relationships, and other information from which a cost basis could be inferred. Thus, the LCA report is generally confidential.
By contrast, the EPD is a summary of results from the assessment, and will usually not reveal that proprietary information. Demonstrating exceptionally good environmental performance may require disclosing more data about certain critical inputs (such as cement or post-consumer recycled content). If desired, you can voluntarily increase (but not decrease) an impact to avoid disclosing proprietary information; the relative value of confidentiality vs. a more favorable impact comparison is a business decision.
Third Party Verification
A third party verifier, who is typically an life-cyle analysis professional approved by the Program Operator, must verify the LCA report that was used to generate your EPD. The verifier checks that the report adheres to the LCA standards and PCR rules. Some service providers offer tools that generate pre-verified reports; however, it does not relieve an EPD from being fully third-party verified.
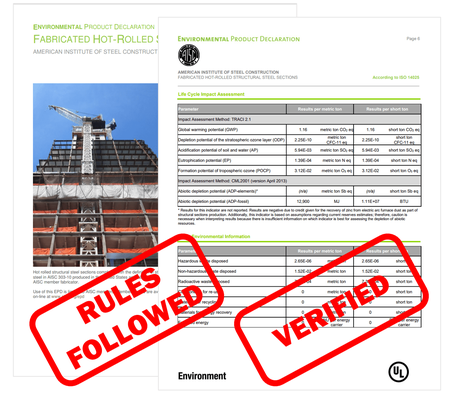
Publishing your EPD
Once the EPD is verified, it can be registered with a Program Operator and published in a variety of formats, including traditional PDF format(s) and digital format(s) such as OpenEPD and ILCD+EPD. Digital publication is generally faster, less expensive, and easier to keep up to date than paper or PDF formats.
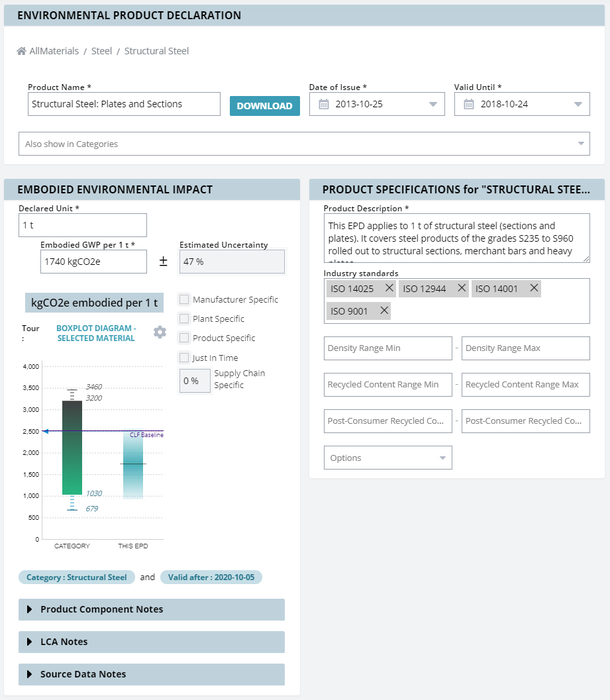
Improving your EPD results
Key ways to improve your EPD results include
- Reducing the Burden of Doubt through transparency
- Reducing direct emissions
- Influencing your supply chain
- Performance-based specifications
Reducing the Burden of Doubt
Uncertainty bounds in EC3 represent the potential difference between what is in a declaration and the actual emissions to make the particular product used in a project, at the actual place and time, if measurement were perfect. Uncertainties in LCA estimates vary widely, and can be large. When possible, EC3 shows the uncertainty of each estimate when doing comparisons.
When comparing large lists of declarations, EC3 uses a value which is at least 80% likely to be conservative; this combines the value and uncertainty into a single figure. The difference between the 50% confidence value and the 80% confidence value is termed the ‘Burden of the Doubt’ and can be reduced by making disclosures more specific in terms of the product, manufacturing process, and upstream impacts.
The first step is having a manufacturer-specific EPD, which indicates an EPD based on a particular manufacturing technology and ingredient list. A large manufacturer-to-manufacturer uncertainty is applied when this is not the case (typically to Industry EPDs).
The second step is having a facility-specific EPD, which ensures that a particular manufacturing process, grid mix, and fuel sources are known. In cases where a facility-specific EPD is not practical (e.g. due to distribution), disclosing results that are verified to be from the highest-impact facility in a group is an acceptable way of removing plant-to-plant uncertainty.
The third step is ensuring that the EPD applies to a single product (or, more precisely, to a set of products whose differences are irrelevant to impacts, such as the colour and pattern of a carpet). Many products come in a range of thicknesses, strengths, or treatments that strongly affect their impacts; for example a 4mm membrane has routinely twice the impact of a 2mm membrane. Some categories have declared units that make this easy (e.g. per unit mass, or per unit thermal resistance) while others may require auto-generation of many EPDs.
The fourth step is disclosing specific emissions for the parts of the upstream supply chain that most affect the product’s impact, such as cement in concrete, recycled content in steel, or aluminium source for IGUs. Indeed, many construction products’ impacts are primarily in the supply chain. A product whose impact is 90% from upstream sources and uses industry-average data for those sources is considered almost as uncertain as an industry EPD. If you can work with your supply chain to secure EPDs for the 1-2 most impactful components, that usually eliminates most of the supply-chain uncertainty.
The fifth step is ensuring that the EPD is reissued in a timely way when there are substantial changes in the process. This is nominally required by most PCRs, but in practise the EPDs are seldom reissued in under five years; the drift in underlying factors is represented in EC3 by batch-to-batch variation. Issuing EPDs just-in-time, using an automated process, will eliminate this uncertainty. In some industries, this variation may be naturally quite small; providing BuildingTransparency with evidence of this variation will allow us to set it to a more appropriate value.
Reducing direct emissions
Once you have a system in place to measure emissions by specific facilities and products, it is much simpler to set targets for reduction. There is a large body of literature on how to do this, but measures such as sourcing green electricity, changing fuel mixtures, adding efficiency measures, and carbon capture are among the possibilities. A sustained pareto-type process, possibly coupled with an internal 'shadow price' for carbon emissions, can lead to remarkable results, just as it has for product quality, manufacturing cost, and employee safety.
Influencing your supply chain
Much of the impact of your product may be in the materials you source, such as aluminium, zinc, cement, steel, or wood. While you do not control these directly, as the customer you can have substantial influence over suppliers, either directly or through collective action. Requesting verified declaration of impacts and examining ways to reduce can be highly productive; often suppliers already know how to reduce and require only a business reason to do so.
Performance-based specifications
In some instances, specific functional performance requirements may allow for modifications to the product or its manufacturing process. For example, the environmental footprint of concrete can be reduced by optimizing the time to strength requirements given specific environmental conditions, instead of specifying the exact amount of ingredients up front. You may be able to reduce your product’s environmental footprint using a similar approach - by helping designers specify your products.